Green Steel Market Size and Growth 2025 to 2034
The global green steel market size was estimated at USD 3.70 billion in 2024 and is expected to surpass around USD 279.40 billion by 2034, growing at a compound annual growth rate (CAGR) of 54.10% over the forecast period from 2025 to 2034.
The global green steel market represents a steelmaking segment that produces steel in a manner that is environmentally friendly-large scale carbon emissions from conventional steelmaking are either drastically curtailed or almost eliminated. Green steel is relatively in the limelight because of alternative processes based mostly on low carbon measures whereby hydrogen-based direct reduction, electric arc furnaces running on renewable energy, and carbon capture technologies feature prominently. The need to decarbonize heavy industries and hence fulfil climate test dictates has acted as the chief impetus for this transformation. Green steel, thus, replaces a coal-based method with a cleaner alternative, thereby making steel production clean, which is among those that have the heaviest environmental footprint from the industrial side.
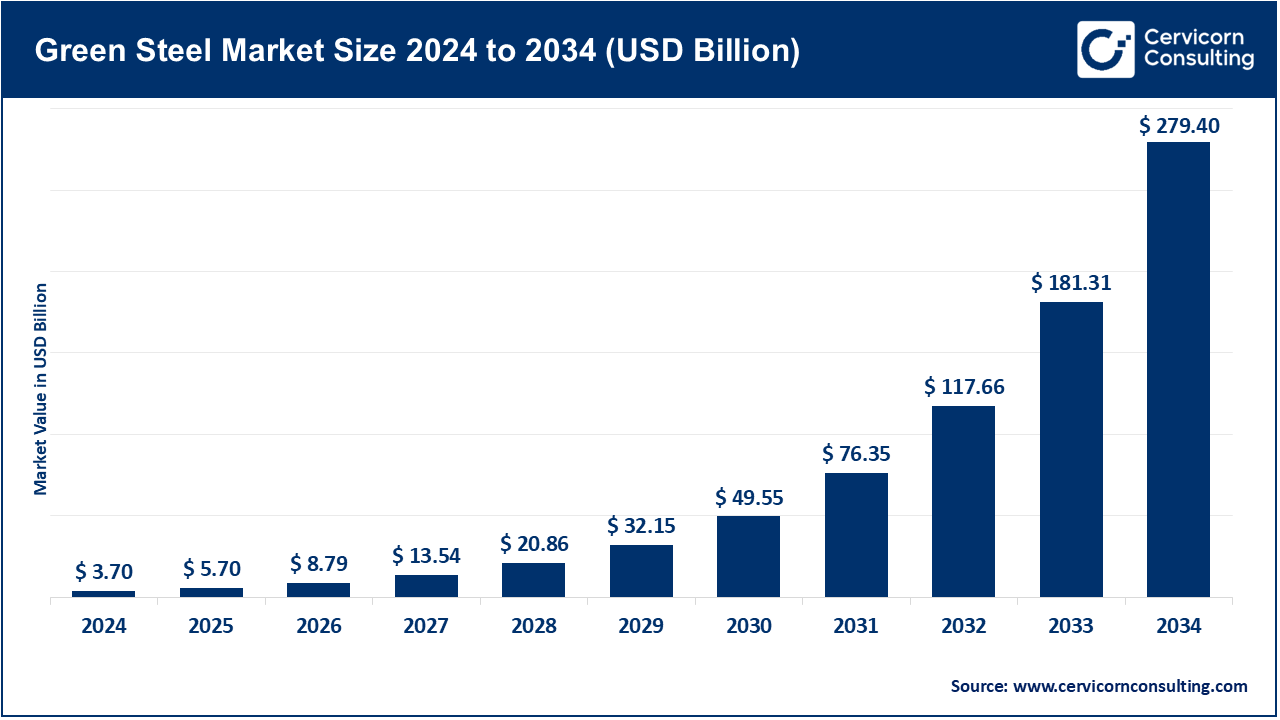
Regulatory and environmental restraints to announce the industrial emissions reduction-remained among the primary factors imposing on the growth of the green steel market. Producers have also been pushed by investors and consumers to shift towards green product types. These industries are preferring low-carbon steel green steel more and more in their measures to build brand recognition and improve their sustainability goals. Through the intervention of green hydrogen production technology and the integration of renewable energy, production along green lines has become more technical and financially viable, thus giving a new pace to the growth of the market. The push for circular economy principles also helps in increasing the usage of scrap-based electric arc furnaces by way of approved material reuse while bringing down the emission load.
A multitude of prospects exists in the market for green steel. There is much room for industrial collaborations, especially among steel producers, energy suppliers, and production technology companies working toward zero-emission solutions. Government incentives, such as tax breaks and funding for green infrastructure, open new doors for project developments and expansion of pilot technologies. Furthermore, the growing number of net-zero commitments from the corporate world within and across industries creates a demand for green steel, a sustainable material. Green steel is also looked upon as a strategic investment avenue by countries and companies that wish to carve a name for themselves as leaders in green technologies. As innovation takes its course and scaling of production follows, green steel will move onto a larger market share: long-term growth in green steel is for the established manufacturers as well as new entrants focused on clean production technology.
Green Steel Market Report Highlights
- By Region, North America has accounted highest revenue share of around 49.9% in 2024.
- By Product Type, the flat steel recorded about 49.8% of revenue share in 2024. The flat segment dominates since these flat steel products find uses in a great number of end-user industries such as automotive, construction, and appliances. Flat steel products like sheets and plates are manufactured into vehicle bodies, structural panels, and machinery that are inclined toward sustainability considerations. Moreover, the decarbonization drive for automotive production and infrastructure development slightly pushes the demand for green flat steel. On the other hand, because of its easy processing, minimal weight, and energy-efficient production routes, manufacturers consider flat steel a prime target for green steel innovativeness and investment worldwide.
- By Production Technology, in 2024, the electric arc furnace (EAF) with renewable energy segment held a revenue share of about 39.1%, this being because of its scalability, fewer carbon emissions, and compatibility with recycled scrap steel. Investopedia Earlier, arc furnaces were mostly used for melting scrap iron for reuse. However, EAFs are highly energy efficient as compared to traditional blast furnaces and can be operated by renewable electricity, bringing down their carbon footprint significantly. The greater availability of renewable sources of energy and pressures to meet sustainability goals are pushing for rapid deployment of EAFs. Besides, costs of production and easy integration into existing steel-making infrastructure make a preferred choice among manufacturers trying to adopt greener methods of production.
- By End-Use Industry, The automotive sector paid 40.4% of revenue in 2024. The automotive segment is big by virtue of the heavy emphasis industry on sustainability and decarbonization. Being so, the big automotive manufacturers are integrating green steel more and more as a means of curbing their own carbon footprint and by so doing answer the call of ever-stringent emissions regulations. This green shift toward electric vehicles further increases green material requirements for vehicle frames, bodies, and components. Market growth is further accelerated by partnerships between automotive OEMs and producers of green steel. With consumers demanding greener vehicles and climate targets being set worldwide, the automotive sector remains firmly ahead in integrating green steel into its production and supply chains.
Top Countries in Green Steel Production
Countries |
Share (%) |
China |
54% |
India |
6.30% |
Japan |
5.10% |
USA |
4.60% |
Russia |
4% |
Green Steel Market Growth Factors
- Stringent Carbon Emission Regulations: Governments and regulators from around the world are restricting carbon emission standards so that working against climate change may be addressed. Being among the major industrial emitters of CO2, the steel industry faces unlawful mounting pressures to reduce its environmental footprint. These regulations push companies to decommission the traditional blast furnace pathway for other low-emission alternatives, such as electric arc furnaces (EAFs) powered by renewable energy or hydrogen-based direct reduction processes. Such policy instruments provide financial incentives to industries to invest in clean technologies, making regulatory compliance a fierce driver for the expansion of the green steel market.
- Rising Demand for Sustainable Construction: Going green is a universal trend followed by construction companies. Since green steel is supposed to produce less carbon emissions, the trade is best suited for infrastructure and real estate projects, as environmental concerns are the project's common goal. So, developers and governments have started incorporating low-carbon materials in their building codes and procurement guidelines. With the fast pace of urbanization, both in developed and developing nations, the need for sustainable materials is also growing. Demand from green steel at residential building construction level, commercial complexes, and goods infrastructure projects involving roads, bridges, and transit systems has been generated.
- Corporate Net-Zero Commitments: Corporations attaining national status or any steel suppliers and those using steel, viz., automakers and appliance manufacturers, consider net zero carbon emission targets. Yet, all these commitments entail a reassessment of supply chains and raw material sources. It is in this respect that green steel is embracing childhood as a special material for carbon foot printing of finished products. For example, automakers are forging partnerships with green steel producers to guarantee sustainable production all the way down the value chain. Such corporate aspirations for sustainability impose a ripple effect across the industries, thereby catalysing investments into green steel technology and propelling traditional steelmakers into research and decarbonization of their operations.
- Technological Advancements in Steelmaking: The progress in technology has been making feasible and competitive in cost the production of green steel. Until now, low-grade steel-making methods driven by emissions from the high-grade processes are being remodelled with high-grade emissions from techniques such as H-DRI, CCS, and renewable power-based EAF. The introduction of scalable green hydrogen infrastructure and improved renewable energy integration are two more backbones of this transition. These technologies offer good emission reduction, improved operational efficiency, and better use of resources. With the cost of Production Technology exhibiting a downward trend and increased proof of commercial viability from pilot projects, more steel producers have begun to invest in clean alternatives, thus becoming the major drivers for green steel market growth.
Green Steel Market Trends
- Dominance of Electric Arc Furnaces (EAFs) and Scrap-based Recycling: In the green steel making, the move from traditional blast furnace methods towards electric arc furnaces is a defining trend. An electric arc furnace uses electricity to melt recycled scrap steel, thus saving a lot of carbon emissions compared with the more conventional form of steel making. The process fits well into the circular economy template to enhance resource efficiency and reduce waste. More and more manufacturers are investing in EAF because these furnaces require less raw material and can also be energy efficient when powered by renewable sources. The increase in available steel scrap coupled with enhancements in furnace efficiency is speeding up the transition. Sustainability is fast gaining footing as a huge differentiator, so respective industries are orienting toward the scrap-based pathway more and more. Still, ensuring the logistics of scrap quality and scrap quantity is a practical challenge. Notwithstanding, with appropriate technological enhancements and policy pygmies-risk to meet carbon reduction objectives, EAFs are emerging as the choice Production Technology pathway towards industry decarbonization.
- Rising Adoption of Hydrogen-based Direct Reduction (H-DRI): Hydrogen-based direct reduction is one of the emerging and revolutionary green steel-making processes. It substitutes the use of fossil fuel with green hydrogen for iron extraction from ore, thereby practically hitting the carbon emission hammer. The steel industry considers H-DRI the pathway for deep decarbonization. Companies and governments are in the phase of piloting projects and building infrastructures for hydrogen supply chains. The avenue of producing steel with practically zero carbon footprint when based on renewable power is what markets the option. As the climate goals have been rendered more ambitious, the need for scalable, clean technologies such as H-DRI has increased in intensity. Though the Production Technology is currently under evolution, it stands as the symbol of long-term commitment of the industry toward green transformation. Its success or failure may make or break depending on the availability of hydrogen, technological maturity, cost competitiveness, and several other dynamics. In short, H-DRI is a future-oriented employment in the global quest for greener steel production.
- Strong Policy and Market Drivers Aligned with Automotive and Construction Sectors: Policies and market developments precipitate the advance of green steel, particularly in sectors bearing a high impact such as automotive and construction. Governments impose environmental regulations, set up carbon pricing mechanisms, and offer incentive schemes encouraging the industries to adopt low-emission materials. At the same time, these end-user sectors elevate sustainability standards by demanding low-carbon-footprint steel to satisfy consumer expectations and pertinent corporate ESG agendas. Automotive OEMs, particularly for electric vehicles, tool up their supply chains with green steel to sustain the product in totality. In construction industries, developers increasingly strive to use eco-compatible materials for green building accreditations and low-carbon compliances. These sectors therefore form a powerful demand side that motivates steel producers toward innovation and adaptation. With the blend of regulatory setup and demand-side pressure gaining prominence in the constraints of embedded emissions, green steel is slowly gaining acceptance.
Report Scope
Area of Focus |
Details |
Market Size in 2025 |
USD 5.70 Billion |
Expected Market Size in 2025 |
USD 279.40 Billion |
Projected CAGR 2025 to 2034 |
54.10% |
Dominant Region |
North America |
Region with the Strongest Growth |
Asia-Pacific |
Key Segments |
Product Type, Production Technology, End-Use Industry, Region |
Key Players |
SSAB, Emirates Steel Arkan Group, Outokumpu Oyj, Swiss Steel Group, ArcelorMittal, China Baowu Group, Salzgitter AG, H2 Green Steel, Nippon Steel Corporation, Nucor Corporation |
Green Steel Market Dynamics
Market Drivers
- Corporate Net-Zero Commitments: Global companies are increasingly subject to the pressure of shrinking their carbon footprints. Accordingly, many companies have set infinity net-zero targets for 2030, 2040, or 2050. From there, they require greener supply chains-the acquisition of green materials such as green steel. More so for industries with high demands on materials - automotive, construction, consumer electronics, and white goods manufacturing. For example, with carbon-free or low-carbon steel for use in vehicles, companies such as Volvo and Mercedes-Benz have made pledges toward that objective. These companies see green steel as important not just for complying with laws, but equally important for brand-building and setting themselves apart from others in the eyes of the consumer. Steel producers are responding to this pressure by investing in green technologies that will thus lead to an increase in the usage of hydrogen-based processes and renewable energy. This trend is quickly turning green steel from a niche product to a supply chain requisite.
- Government Incentives and Funding Programs: Governments worldwide are providing several targeted incentives to speed up the green transition in the steel industry apart from environmental laws. These incentives include tax rebates, direct subsidies, R&D grants, and concessional loans for plants adopting technologies that reduce carbon emissions. In Europe, North American, and Asian countries, pilot projects are being funded, and green hydrogen hubs are being set up for clean steelmaking. Public-private partnerships are critical in de-risking the process and encouraging early-stage technology adoption. Funding thus reduces transition costs and risks that steelmakers incur when departing from conventional blast furnaces to hydrogen- or EAF-based technologies. These programs are especially critical to keep green steel cost-competitive with traditional steel that has been advantaged by economies of scale for a long time now. Government support effectively lowers both capital and operational barriers, thus acting as an important driver of innovation and manufacturing capacity growth in green steel.
- Growing Investor Pressure and ESG Focus: The financial sphere is becoming aligned with the E, S, and G in ESG, and investors are therefore disposed toward companies that have carried strong sustainability credentials in their business practices. Steel companies with emissions comparable to those in the high emission category will face pressures from stakeholders like the shareholders, banks, and asset managers to start decarbonizing or be divested from. Environmental-conscious investors track environmental impact metrics, such as carbon intensity per ton of steel produced. Consequently, companies that actively engage in green steel production are deemed lower-risk and higher in future-proof value, thus marking higher interest for investment. On the other hand, sustainable steel producers are more likely to be included in ESG-related indices and funds, which provides enhanced visibility and access to capital avenues. This presently investor-driven demand for low-emission manufacturing is compelling traditional steelmakers to upgrade their processes. Thus, the transition to green steel is more a financial necessity than an environmental one, with ESG factors strongly influencing market change.
Market Restraints
- Limited Availability of Green Hydrogen: Green hydrogen is a vital element for green steel production, especially in the Direct Reduced Iron (DRI) processes. However, since the industry of hydrogen itself is at a very nascent stage and because electrolysers used in extracting hydrogen from renewable energy sources are cost-prohibitive, the global availability of green hydrogen remains a challenge. Most hydrogen produced today is derived from fossil fuels (grey hydrogen), which completely contradict the very concept of carbon-free steel making. Hence, this shortage creates a big supply bottleneck for green steel producers that require steadfast provision of hydrogen at a large scale to be able to run their operations consistently. The transportation and storage of green hydrogen remain a technically challenging and costly affair, further impeding utilization. Thus, on account of lack of sufficient investment and policy, this limits the ramp up of green hydrogen infrastructure, thereby restraining steel sector to fully transition from coal-based methods and consequently becoming the biggest limitation on the development of the green steel market.
- Long Payback Period for Investments: Besides the transition to green steel needing some serious capital investments into new technologies, they include hydrogen-based DRI plants, electric arc furnaces (EAFs), renewable energy systems, and the whole carbon capture infrastructure. These are multi-billion-dollar investments, with payback times stretching into a decade or more unless carbon pricing or subsidies work their magic. This often means risking money for steel producers in emerging nations or in low-margin markets. Companies would most probably resist investing without some form of long-term stable policy framework, demand assurance, or market incentives. Meanwhile, green steel carries a premium to date-but who knows if this will survive in the long haul? That is one reason why investment in green steel remains unattractive; the second is the uncertainty, which slows the transition of the industry and positions the long ROIs as a big financial barrier.
- Logistical and Storage Limitations: Supporting infrastructure for green steel production is rather complex and remains underdeveloped, especially for logistics and storage. Hydrogen, a key green steel feedstock, is notoriously difficult to store and transport due to its low energy density and flammability. Storage options include high-pressure compression, cryogenic temperatures, or chemical carriers, each imposing costs and operational hurdles. Likewise, renewable energy--used for electric arc furnace operations and electrolysis-comes with unpredictability. So, grid interfaces and energy storage must be made advanced enough such that a steady supply is maintained. Quite a few industrial regions are ill-equipped for this, thus reducing the number of places where green steel plants could indeed be set up. Leaning on unequipped storage and logistics, the green steel supply chain largely and painfully crystallizes inefficiencies, delays, and hazards-were all to redundancy-industry growth and competitive ability considered from the global point of view.
Market Opportunities
- Scaling Hydrogen-Based Steel (Green Hydrogen DRI): The transition to hydrogen-based steelmaking provides a great opportunity to decarbonize one of the most emission-prone industries. Using green hydrogen instead of traditional coal for the reduction process allows one to realize drastic cuts in greenhouse gases. The hydrogen DRI method of steelmaking is gaining prominence with the drop in price for renewable energy and push from governments for cleaner technologies. With global hydrogen infrastructure on its rise, this steel product type is in place to come into mass production. Early investors in hydrogen DRI can create their image as one of the earliest front runners in green steel and thus be able to embark on long-term supply contracts with customers adhering to green principles. Additionally, coupling hydrogen with renewable energy can bring enhanced efficiencies, lowered carbonization on fossil fuel usage, thus faster the overall process of industrial decarbonization. This opportunity exists not just for greener steelmaking but also in transforming the entire value chain to a low-carbon, future-ready system.
- Expanding Electric Arc Furnace (EAF) & Scrap-Based Circular Production: Electric Arc Furnaces (EAF) present a great opportunity for green steelmaking that utilizes recycled scrap instead of raw iron ore. Such a process drastically brings down the consumption of energy and in consequence reduces carbon emissions accordingly. Due to abandonment caused by urbanization, an increased supply of steel scrap is placed, making for a sturdy feedstock for EAFs. These furnaces being coupled with renewable energy sources will thus make the entire process even more eco-friendly. As stakeholder pressure to move to circular economy lines mounts, steelmakers stand to gain as they move ahead with expansions in EAF capacity and plant modernization for energy efficiency. Introduction of smart technologies such as AI for predictive maintenance and scrap sorting will improve efficiency and reduce costs. These are the least-waste, resource-sustainable solutions. Producers achieving this opportunity can thus assist in global decarbonization objectives and become more responsive to customer demands for green products, ultimately becoming more resilient in the rapidly changing regulatory and market environment.
- Tapping into High-Growth End-User Sectors: Green steel establishments have much room for growth if they target these demanding sectors that actively seek adoption of low-carbon materials. For example, the automotive industry is currently under pressure to reduce emissions in the entire supply chain, including steel components. Hence, the construction industry is moving towards greener materials to satisfy sustainable building standards and achieve certification goals. Infrastructure projects, particularly those attached to renewable energy-granting application such as wind turbines and solar arrays-are also low-carbon steel solution demanding ends. Such sectors are not only high volume but are also willing to pay a premium for such sustainably sourced materials. It is thus important for the green steel producers to link their product offering with sustainability goals of these industries so as to stain long-term contracts and enter emerging markets. With the increase in environmental regulations and awareness-with-consciousness-raising-who-awareness-about-ecological-footprints, these sectors will grow exponentially in demand, presenting an opportunity for manufacturers who intend to fill the void with a clean, New Age steel solution.
Market Challenges
- Technological Readiness and Scalability Issues: Whether down the line, landowners, residents, and businesses may well find that some of their rights are expropriated for very large steel plants and green steel and may eventually be suitably compensated for the rights they've given up. The technology has so far been down the drawing board or in a laboratory or pilot plants: hydrogen-DRI, molten oxide electrolysis, and advanced stages of carbon capture are all just being developed or at that stage. To add to their woes, these applications still suffer from numerous issues, from integration with existing plants, efficiency losses, operational stability on plants, and so on. Furthermore, going from laboratory or pilot-scale demonstration to full industrial implementation takes decades of capital investment and engineering development. There is a huge risk to major steelmakers in moving to such a newer system-it covers production disruptions and the return on investments being uncertain-and the pace of innovation may not coordinate with global climate target-creating a gaping divide between technological aspiration and practical deployment. Few will put money and time into such transformation until the solution comes through in proven scale, which will put speed to green steel on snail-track.
- Supply Chain and Raw Material Constraints: Producing green steel is highly dependent on getting raw materials, primarily high-grade iron ore and anything along the lines of quality scrap steel, coupled with renewable electricity or even green hydrogen. However, such inputs do not come easy in all corners of the world. For example, high-grade iron ore that is supposed to be used for hydrogen-based DRI is less abundant and more expensive than its conventional counterpart. The scarcity of scrap is generally tied to poor or developing recycling infrastructure. Moreover, if renewable energy or hydrogen needs to be transported to the site of production, the logistical and infrastructural challenges can become a hindrance, particularly in isolated or heavy industrial areas. Even the make-up of supply chains for green steel demands ample coordination between mining companies, energy providers, hydrogen producers, and steelmakers. A hiccup or constraint at any stage of this chain can either stall production or render it very expensive. Being so linked through its dependencies, it becomes an ever-increasing problem to tackling an assured and large-scale supply of materials essential to green steel and thereby the major factor hindering its widespread adoption.
- Customer Willingness to Pay Premium Prices: Demand is certainly one of the largest challenges to the growth of green steel production. Buyers are simply not ready to absorb the higher prices. With green steel, however, the costs involved are sometimes astronomical. Such costs may include higher-priced green hydrogen and renewable energy, or charges for new infrastructure. Despite the mention of big business entities planning to decarbonize their supply chains, sectors like construction, manufacturing, and automotive, in speculated situations, are extremely price competitive and work ever so slightly on meagre margins. These industries do not want to pay more for green steel unless forced to do so by regulation, tax incentives, or consumer pressure. Cost concerns are more important in the emerging markets, thereby further depressing demand. Without a guaranteed floor for these extra investments, steel mills will find it increasingly difficult to forge ahead. Closing this gap between production costs and buyer acceptance will require coordinated policy interventions, strong ESG commitments, and possibly green procurement mandates to stimulate demand for low-carbon steel products.
Green Steel Market Segmental Analysis
Product Type Analysis
Flat Steel: The flat steel segment has held leading position. Flat steel is a generic term for steel products rolled into flat shapes like sheets, strips, and plates. Because it is versatile and strong and can be easily fabricated, in the green steel market, flat steel finds applications in transport (automotive), home appliances, civil constructions, and shipbuilding industries. With the increasing demand for sustainability, manufacturers are adopting green steel in flat form to offset big carbon footprints in large applications. Flat steel is among those industries that gain enormously from green production methods such as electric arc furnaces operated by electricity from renewable sources. It is still a major ingredient in green infrastructures and in low-emission vehicles. Commercial procurement of low-return carbon flat steel is, however, rapidly skyrocketing with OEMs and government-infrastructural projects that strongly focus on ESG objectives. Flat steel, given its diverse industrial applications and plethora of environmental regulatory compendia, all dictates into the greener steel world and embodies its leading front in the cross-industry thrust for a decarbonized material.
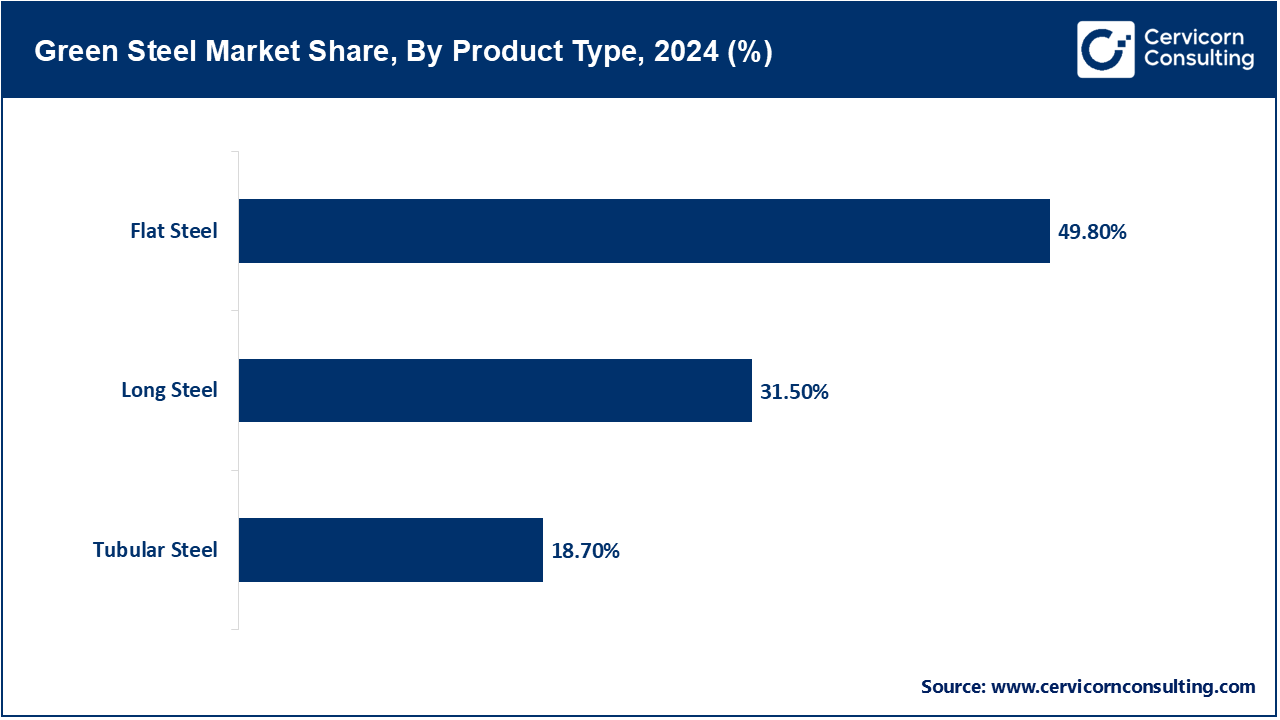
Long Steel: Long steel products include bars, rods, rails, and structural sections used chiefly in construction and engineering projects. Being used in the production of sustainable buildings, bridges, rebar for concrete structure, and heavy industries, long steel products are important for green steel. With nations all over the world promoting green buildings coupled with net-zero construction targets, the demand for low-carbon long steel is on the rise. These products are more environmentally friendly if produced through recycling routes such as scrap-fed electric arc furnaces instead of being produced in blast furnaces. Long steel proves useful for renewable energy by providing supports for wind turbine towers and solar panels. As the construction industry turns toward lowering the embodied carbon within materials, this segment grows. Being sturdy and recyclable, long steel is one of the very few materials deemed suitable for green construction; hence, long steel sits right in the middle of the transition of the construction sector toward sustainability.
Tubular Steel: Tubular steel encompasses steel pipes and tubes used for fluid and gas transportation as well as structural applications. In the green steel market, tubular products are movers in the energy (especially hydrogen and renewables), construction, and automotive sectors. With the initiation of clean energy on the global front, tubular green steel is gaining importance in the erection of hydrogen infrastructure, wind energy, and sustainable water distribution. Green steel pipelines fabricated with truly low carbon processes will curb the environmental footprint of symbolically important large-scale infrastructure and industrial projects. The segments attract recycled steel as well as low-emission production processes, thereby conforming to corporate and regulatory targets to cut down carbon emissions. Tubular products are being increasingly used in transport systems designed for sustainability, including components for electric vehicles and infrastructure for public transit. In line with rising demand for environmentally responsible pipelines and structural supports, tubular steel illustrates a growing and innovative application area within the green steel ecosystem.
Production Technology Analysis
Hydrogen-Based Direct Reduced Iron (H-DRI): The H-DRI represents an avant-garde green steel technology aimed at substituting fossil fuels with hydrogen as the reducing agent to strip oxygen from iron ore. The process emits no carbon dioxide and produces only water vapour. H-DRI is followed by sponge iron melting usually in an electric arc furnace, which is operated on green electricity, thus constituting a low-emission way to make steel. This technology is increasingly gaining recognition with the global urgency in decarbonization and the large regional investments in green hydrogen infrastructure. The high cost and scarcity of hydrogen pose constraints, but as hydrogen becomes cheap, we should be looking at H-DRI becoming the favourite process in green steelmaking.
Molten Oxide Electrolysis (MOE): In essence, MOE when given the status of emerging green steel technology, specifies the electrolysis procedure by which iron ore is directly converted into molten iron without having to use any type of carbon reductants. This wonderful system passes electric currents through molten oxides, thereby breaking the iron-oxygen bonds and releasing oxygen as one of the by-products instead of carbon dioxide. The high-purity steel and the absence of coke or coal are advantages given by MOE. Yet, as with many technologies in the developmental phase, it faces problems of energy consumption rates, material durability under proceeds of extreme heat, and imbalance concepts regarding its scale of production. Given the accessibility of renewable electricity, MOE holds the possibility of bringing a big transformation in sustainable steelmaking.
Carbon Capture, Utilization, and Storage (CCUS): CCUS technology focuses on sequestering carbon dioxide emissions arising from conventional steel production, through a blast furnace, for either underground storage or for conversion to chemical products. Thus, unlike direct zero-emission steelmaking, the CCUS technology can reduce substantially the carbon footprint of traditional steelmaking processes. It is considered a transitional measure, permitting existing plants to comply with climate regulations without being refitted completely. The feasibility of CCUS will thus depend upon capture efficiency, storage safety, and cost-effectiveness. As governments increasingly offered incentives and set targets for emission reduction, CCUS is being increasingly considered within hybrid green steel strategies compared to scenarios emphasizing sustainability more than operational continuity.
Electric Arc Furnace (EAF) with Renewable Energy: In the production of steel, the EAF method finds widespread acceptance. Here, scrap steel or direct reduced iron is melted by means of electric arcs. When renewable electricity (wind, solar) is used for running electric arc furnaces, however, it becomes a low-emission process, suitable for green steel production. Its main advantages are in its flexibility, energy efficiency, and recycling of scrap materials. Several developed markets have seen commercial enterprises operating on EAF with renewable energy. This method follows circular economy principles and works best in urban places, where scrap steel collection systems have matured. Its application, however, depends upon the availability of scrap and the integration of renewable grid, both of which vary from region to region.
Biomass-Based Reduction: Reduction based on biomass substitutes coal or coke for carbon sources derived from biomass (such as charcoal) in the reduction of iron ore. It becomes carbon-neutral, considering if the biomass is sourced in a sustainable manner and is regrown to absorb the CO2 released. This should be especially appealing in regions where biomass resources are in abundance. Though this approach may lower life cycle emissions, issues encountered are supply chain logistics, land-use conflicts, and lower calorific value when compared to coal. Biomass reduction can act as the bridge technology for decarbonizing existing blast furnace operations, and a complementary one for other green steel routes. Improvement in technology and sustainability certification are key to scaling the solution.
End-Use Industry Analysis
Automotive: The automotive segment has accounted highest revenue share. Automotive is the foremost consumer of green steel establishment toward the goal of sustainability and regulatory mandates for carbon reduction. Electric vehicle manufacturers and traditional automakers have started integrating green steel into the manufacturing lines to make sure to lower the carbon footprint on their vehicles of the chassis, body panel, and structural components, which essentially have the same application as conventional steel but are far less in emissions during their production. The increasing consumer awareness and ESG commitments amongst producers is leading to cooperation between automakers and steel producers for setting up long-term supply chains for green steel. This sector is expected to have a strong growth track because of the global movement towards clean vehicle transit and life cycle emission reductions in vehicle manufacturing.
Construction: Green steel has momentum in the construction setup, especially for commercial and infrastructural projects looking for LEED certification or net zero goals-building frame, rebar, beam, and cladding materials. Governments and private developers alike are promoting sustainable construction, thereby applying higher demand for eco-friendly construction materials such as green steel. Green steel is compatible with green building codes and supports lifecycle sustainability, helping to reduce emissions associated with urban development. In keeping with commitments on climate change and the circular economy, new high-rises, bridges, and public infrastructure increasingly specify green steel. Construction demand will go up due to regulations, investor pressure, and long-term cost benefits associated with sustainable materials.
Green Steel Market Revenue Share, By End-Use, 2024 (%)
End-Use |
Revenue Share, 2024 (%) |
Automotive |
40.40% |
Construction |
28.10% |
Energy & Power |
10.20% |
Manufacturing |
15.30% |
Others |
6% |
Energy & Power: The global energy and power sector sees high-strength steel used as a construction material in such renewables as wind and solar: wind turbine towers, solar mounting structures, and transmission towers. With a global tilt toward renewable energy and decarbonizing the power grid, green steel stands out as the most appropriate environmentally conscious material that meets low-carbon goals. Energy majors have started sourcing green steel into their supply chains to meet ESG commitments and regulatory expectations. On a much larger scale, hydrogen and green ammonia projects will demand eco-friendly steel in huge volumes for storage tanks, pipelines, and platforms. Thus, a strong long-term demand for the green steel in this sector is being created through the energy transition.
Manufacturing: One steel is for manufacturing industries to build up machinery, tools, components, and infrastructure for plants. Across manufacturing, green steel is being taken up in an ever-accelerating way, as companies of all sectors-from consumer goods to heavy machinery-are seeking to reduce Scope 3 emissions. Manufacturers are now looking to integrate green steel into product design to substantiate their sustainability claims and add value to their brands. Companies in sectors such as electronics, appliances, and industrial machinery are increasingly sourcing materials with low emissions to satisfy customer and regulatory demand. This segment is also influenced by carbon pricing, with companies seeking to reduce the embedded emissions in the goods they export. More green steel usage will thus spread across different manufacturing verticals as sustainability reporting grows toward standardization.
Others: This "Others" segment consists of applications such as consumer goods, shipbuilding, agricultural equipment, and defence. With a lower tonnage as compared to the other segments, these industries still foster the demand for green steel in a big way. An example in this context is consumer electronics and white goods, where the use of green steel in casing or structural components is gaining traction to cut down on lifecycle emissions. Green steel is being felt as an alternate with a lesser carbon footprint for maritime transportation in shipbuilding. Through government sustainability initiatives, the defence and aerospace sectors are beginning to adapt green materials for bases, equipment, and vehicles. Agricultural machinery and tools are also being conditioned towards more environmentally friendly materials. This diversity of applications reveals the cross-sectoral capacity of green steel and the immense sustainability awareness across the whole industrial spectrum. As global carbon accountability spreads, even those users of steel that traditionally were relegated to very low tonnage are seeing some value in the switch to green alternatives, gradually paving the way for comparatively small-scale dispersal.
Green Steel Market Regional Analysis
The green steel market is segmented into several key regions: North America, Europe, Asia-Pacific, and LAMEA (Latin America, Middle East, and Africa). Here’s an in-depth look at each region.
Why is the North America region leading the green steel market?
- The North America green steel market size was estimated at USD 1.85 billion in 2024 and is expected to reach around USD 139.42 billion by 2034.
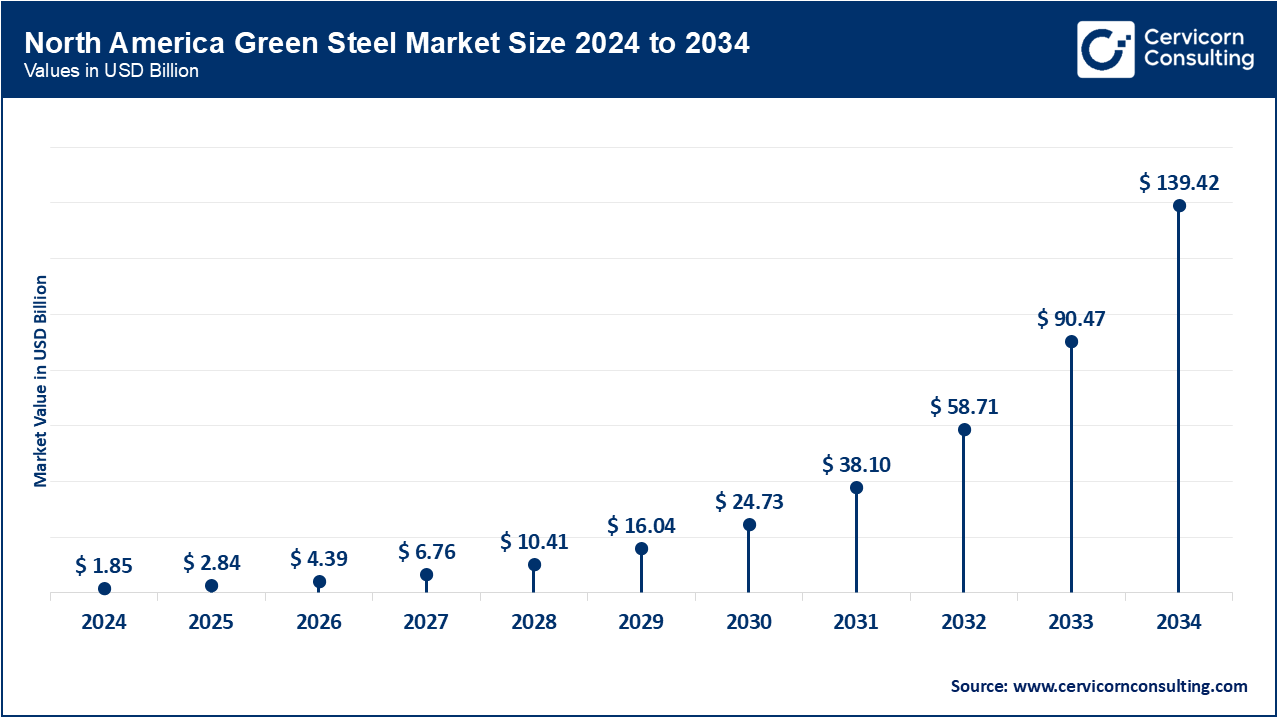
The North America region has therefore been charging ahead in green steel, with regulatory pressure on carbon emissions gaining pace, followed closely by the manufacturers and automotive sectors flying the sustainability flag. There are upward trends for green hydrogen production and electric arc furnace (EAF) technologies in the U.S. and Canada, both considered significant actors in the green steel ambience. Steel-making units in the country seem to be propagandized under influence of tax regimes, clean energy policies, and so on towards greener alternatives. Automotive OEMs and construction companies, however, need the greener steel to support their ESG objectives and meet requirements given by the consumers. The partnerships between the big steel houses and renewable energy providers are coming up and getting stronger. But on the downside, high upfront costs, coupled with some level of reliance on the traditional steel-making process, remain stumbling blocks. The region, with the ever-rising awareness and policy support across decarbonization goals, is expected to swell to a very large green steel demand contributor.
What are the key drivers of the green steel market in Europe?
- The Europe green steel market size was valued at USD 0.92 billion in 2024 and is expected to hit around USD 69.29 billion by 2034.
Europe maintains supremacy over the global market due to rigorous environmental regulations, high carbon prices under the EU ETS, and strong political will towards net-zero emissions by 2050. Germany, Sweden, and the Netherlands are leading countries where companies such as SSAB, ArcelorMittal, and Salzgitter AG are taking the first steps in hydrogen-based DRI and other low-carbon technologies. The Green Deal of the European Union and the coming into being of the Carbon Border Adjustment Mechanism (CBAM) have fast-tracked the move towards sustainable steel production. In addition to this, both private and public sectors promote green metallurgy innovations with investments. The demand from industries downstream is robust, especially from automotive, construction, and infrastructure, which are put under pressure to decarbonize their supply chains. In contrast to other geographies with lower production costs, the European green steel market gets an advantage from the policy-driven structure to act as a catalyst for global green steel adoption.
What makes Asia Pacific the fastest-growing region in the green steel market?
- The Asia-Pacific green steel market size was reached at USD 0.75 billion in 2024 and is projected to grow around USD 56.44 billion by 2034.
Owing to rapid industrialization, immense infrastructure development, and enhanced environmental consciousness, the Asia-Pacific is the fastest-growing region. Countries such as China, Japan, South Korea, and India are increasingly focusing on the decarbonization of their steel sector-the one with the highest carbon emissions. Being the largest steel producer in the world, China has set targets for peak carbon emissions and is also investing in hydrogen-based steelmaking technologies. Japan and South Korea are pursuing research in carbon capture and green hydrogen integration. India, with its growing population and steel demand, is now moving towards green steel pilot projects where the government-backed foreign collaborations are aiding. The exports are further driving the growth in the region as in demand territories for green steel. Against the attempts to transit to a greener route for steel production stand the high upfront investment costs coupled with traditional coal-based blast furnaces. With these factors, strong economic momentum and supportive policies are well poised to imbibe Asia-Pacific with transformative intent in the green steel landscape.
Green Steel Market Revenue Share, By Region, 2024 (%)
Region |
Revenue Share, 2024 (%) |
North America |
49.90% |
Europe |
24.80% |
Asia-Pacific |
20.20% |
LAMEA |
5.10% |
What are the key trends shaping the green steel market in LAMEA?
- The LAMEA green steel market size was valued at USD 0.19 billion in 2024 and is anticipated to reach around USD 14.25 billion by 2034.
LAMEA is slowly but surely emerging market. In Latin America, countries such as Brazil and Chile are pursuing green hydrogen projects to facilitate green steel production. Brazil would boast a fine renewable energy backdrop, thus befitting biomass and hydrogen-based DRI technologies. The Middle East is tapping its solar-energy potential into hydrogen production, with countries such as Saudi Arabia and the UAE launching green industrial projects so that their economic diversification strategies are complemented. Green steel in Africa is still in its infancy but is promising with increased foreign investment and regional partnerships. LAMEA faces constraints, such as lack of infrastructure, an obsolete knowledge-base when it comes to technology, and fractured policy environments. Having said that, the region does hold long-term potential to arise when global steel importers begin to demand low-carbon production options.
Green Steel Market Top Companies
Recent Developments
- In Sept 2024, Tata Steel and Her Majesty's Government signed the Grant Funding Agreement of £500 million for the realization of the company's ambitious £1.25 billion green steel project at Port Talbot steelworks in Wales, thereby giving a tremendous respite to the British industry. Being the biggest investment in the UK steel sector for the past few decades, IAG stands to become the precursor for installing a highly touted EAF, along with saving 5,000 jobs, reads the media release issued by the company on a Wednesday.
- In February 2024, Salzgitter Flachstahl GmbH (Salzgitter), a subsidiary of Salzgitter AG, which is among Germany's leading steel and technology groups, and the generation wing of Octopus Energy Ltd., have signed a long-term Power Purchase Agreement (PPA) for the future production of green steel. The PPA was signed with the assistance of the Pexapark advisory team, whereby Octopus, which manages a green energy project portfolio to the tune of €7 billion, shall deliver clean electricity to Salzgitter, generated from the solar farm at Schiebsdorf in Brandenburg, Germany, amounting to 126,000 MWh for 10 years.
- In Jan 2022- H2 Green Steel announces the signing of definitive debt financing agreements for the sum of €4.2 billion as project financing, raising further equity capital of €300 million over and above the amount previously announced, totaling €2.1 billion. The company has also been awarded a grant of €250 million from the EU Innovation Fund and thus funded nearly €6.5 billion for the world's first large-scale green steel plant in Northern Sweden, which is currently under land acquisition.
Market Segmentation
By Product Type
- Flat Steel
- Long Steel
- Tubular Steel
By Production Technology
- Hydrogen-Based Direct Reduced Iron (H-DRI)
- Molten Oxide Electrolysis (MOE)
- Carbon Capture, Utilization, and Storage (CCUS)
- Electric Arc Furnace (EAF) with Renewable Energy
- Biomass-Based Reduction
By End-Use Industry
- Automotive
- Construction
- Energy & Power
- Manufacturing
- Others
By Region
- North America
- APAC
- Europe
- LAMEA
...
...