3D Printing in Defence Market Size and Growth 2025 to 2034
The global 3D printing in defence market size was valued at USD 2.87 billion in 2024 and is expected to hit around USD 18.36 billion by 2034, growing at a CAGR of 27.21% from 2025 to 2034. The global 3D printing in defense market is expected to grow significantly owing to rising demand for lightweight, customizable parts, faster prototyping, and reduced supply chain dependency. Defense agencies increasingly adopt additive manufacturing to enhance operational readiness, lower costs, and enable rapid production of mission-critical components in remote or combat zones.
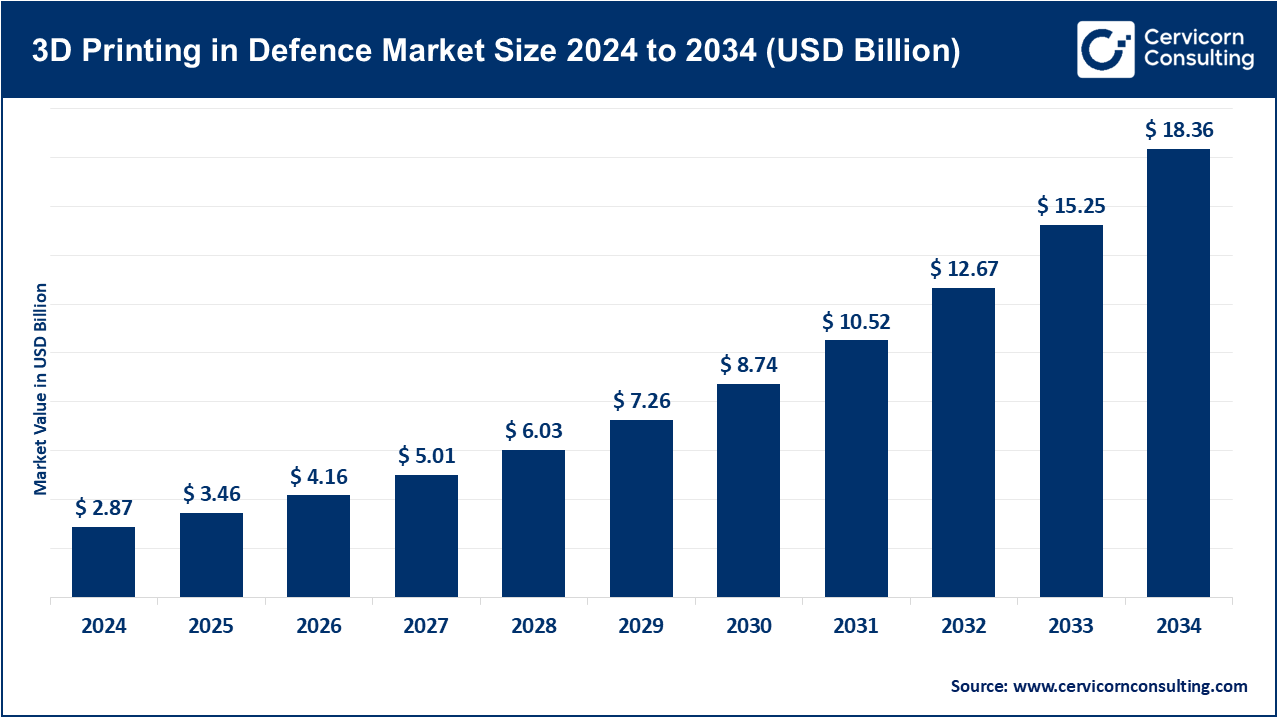
Inauguration of 3D printing technology in the defense sector is a notable evolution in military production and logistics because it incorporates prototyping systems capable of producing urgent parts at any time, any place and accomplishing rapid repairs at the combat zone. Important innovations like metal sintering, use of composites, optimization of designs with artificial intelligence, and even 3D printers which are portable are empowering the defense forces to greatly minimize dependency on supply chains while maximizing adaptability and availability of gear. Uses include customized lightweight equipment for drones, personnel specific gear, hyper sonic weapon components, as well as replacement parts for older systems. These shifts are driven by increased modernization programs from the rising tensions of geopolitical conflict fueled by government spending aimed toward military innovation. This paradigm fosters operational efficiency and increases resilience which enhances decreased downtime centered around decentralized strategic autonomy geared towards agile maneuver warfare.
India’s Defence Revolution
Year |
Values in Crores |
2014-2015 |
1,941 |
2016-2017 |
1,522 |
2018-2019 |
1,0746 |
2020-2021 |
8,435 |
2022-2023 |
15,918 |
2023-2024 |
21,083 |
3D Printing in Defence Market Report Highlights
- By Region, North America has accounted highest revenue share of around 45.4% in 2024.
- By Offering, the printers segment has recorded revenue share of around 42.6% in 2024 due to increased adoption of additive manufacturing in defense for rapid prototyping, reducing production lead times, and enabling on-site parts fabrication during field operations.
- By Process, the powder bed fusion (PBF) segment has recorded revenue share of around 37.3% in 2024 because of its ability to produce complex, high-precision metal components essential for aerospace parts like turbine blades and lightweight structural elements with enhanced strength-to-weight ratios.
- By Application, the functional part manufacturing segment has recorded revenue share of around 54.2% in 2024. This segment dominates as defense sectors prioritize operational readiness through in-house production of mission-critical components, reducing logistics burden and enabling customization in hostile environments.
- By Platform, the land (Hospitals, Field Clinics) segment has recorded revenue share of around 53.5% in 2024 due to deployment flexibility in military medical infrastructure, enabling quick access to customized implants, surgical tools, and prosthetics in combat or remote locations.
- By Component, the technology (Hardware + Software) segment has recorded revenue share of around 47.2% in 2024. Technology leads as integrated hardware and software ensure seamless design-to-production workflows, essential for secure and efficient aerospace and defense-grade additive manufacturing solutions.
- By End-Use, the army medical services segment has recorded revenue share of around 39.7% in 2024 due to demand for customized, on-demand medical devices in combat zones, trauma care solutions, and 3D-printed implants supporting soldiers’ recovery and operational efficiency.
3D Printing in Defence Market Growth Factors
- Decentralized Manufacturing Capabilities: Decentralized field printing presents the capability for military units to manufacture parts locally, where they are needed, and therefore reduce logistics delays. In 2025, the Navy validated with FLEETWERX exercises instances of a containerized metal/ceramic printer capable of manufacturing parts in less than 72 hours even at remote locations. This experiment mirrors and exemplifies the objectives of the 2021 Department of Defense Additive Manufacturing Strategy, which champions resilience in forward-deployed locations. Field reports demonstrate a decrease in lead time for replacement parts down from weeks to days, which represents a vastly improved level of operational readiness. The 2024 National Defense Authorization Act included a provision supporting IP-secure right-to-repair clauses, this will allow purposes of decentralizing manufacture. The strategy of moving manufacture to the location allows the defense forces to minimize vulnerabilities to disrupted supply chains during counter-contested operation if the situation arises. This in turn could sustain mission capability under periods of strategic stress.
- Rapid Prototyping Needs: Defense innovation increasingly relies on swift prototyping via 3D printing during research and design cycles. A 2024 Government Accountability Office (GAO) report noted widespread deployment of additive modeling in weapon system development. The United States Army Rapid Capabilities and Critical Technologies Office routinely uses polymer and metal printing to shorten design-to-test timelines. Recent trials in 2024 cut prototype iteration cycles by over 40%, per internal program reviews. Such acceleration helps counter emerging threats rapidly, with the 2023 DoD Digital Engineering Policy actively promoting digital model-based engineering. Legal frameworks under Section 815 of the 2022 NDAA mandate rapid prototyping for urgent capability needs. This enables agile responses to evolving adversary capabilities without bureaucratic delays.
- Funding Shifts Towards Emerging Technology: Defense budgeting is increasingly reallocated to additive manufacturing initiatives. The FY 2024 DoD budget request included a $0.247 billion investment in additive-manufacturing R&D and pilot activities. Congressional budget justification materials highlight the potential for lifecycle cost savings of 25% through the local printing of parts. The 2023 Congressional Research Service report predicted growth in the acquisition of field deployable printers and materials readiness. Programming Justification Memoranda from the major services noted AM funding priority within the "Next-Gen Manufacturing" line item. The DOD's 2024 National Defense Strategy highlighted how critical it was for the services to modernize their technologies and we agreed with MDAP readiness programming items in the budget. These portions of the violence provide for purchases of advanced printers, materials testing, and operator training. Additionally, the overall budging condition and history were favorable for continued investment headed into 2025 and beyond.
- Miniaturization of components: 3D printing is used to produce lightweight miniaturized components for advanced defense technology. An example, the Air Force Research Laboratory 3D printed a sub-millimeter heat exchanger for hypersonic test articles in 2023. In 2024, the Defense Microelectronics Activity published procurement specifications for printed micro-miniaturized components defined as being under 10 mm. The smaller sizes enable stealthy unmanned aerial vehicles (UAVs), missiles, and hidden sensor systems to be produced without forgoing the operational capacity. Military submissions for patents on printed miniaturized parts increased 35% from 2022 to 2024. The DoD supply-chain review found that miniaturization is key to distributed, secure, and sustainable manufacturing concerns. Acceptance standards defined by MIL-STD-3010 were expanded to include micro-fabricated parts with additive processes. This research supports next generation weapon systems with a diminished weight and overall footprint.
3D Printing in Defence Market Trends
- Recycling/Sustainability regarding materials: Sustainable material use in defence additive manufacturing is gaining traction in terms of policy and budget allocation since 2023. The Defence Innovation Unit ran a pilot of recycled polymer filament to assist in reduced waste within the 20% range - running the pilot with non-critical printing applications. The environmental sustainability measures in the FY 2024 National Defence Authorization Act directed a minimum of 15% recycled input into the additive manufacturing programs. Based on their sustainability reports for 2024, they were able to implement take-back programs and onsite recycling units at the Navy's shore-based manufacturing facilities. The Department of Defense led "Green AM" initiative developed practice standards to promote reusable systems for metal powder earlier this year. Protocols for legal reclamation were later published under DoD Directive 4715.26 in 2023 for procedures related to material recovery operations throughout combat zones. All of this activity will mitigate waste, reduce the logistics of dispersed raw materials, and align everyone within the Department of Defense sustainability plans.
- Digital Twin Adoption: The use of digital twins is expanding in defence additive manufacturing as part of the design and production workstreams. In 2024, the Army Digital Transformation Office was able to use digital twin models to simulate all of the components for field-printed versions of a vehicle, for which they were able to reduce their testing cycles by approximately 30%. In early 2025, the Naval Sea Systems Command leveraged digital twin technology for the valve parts on submarines as part of its New Manufacturing Technology program. The approval of testing standards under the federal acquisition regulations was updated to stipulate digital lineage for additive components (e.g. ASTM F3091-21). The 2023 DoD Digital Engineering Strategy cites extended reality twins as central to model-based systems engineering. Legal provisions in the 2024 NDAA strengthen data integrity requirements for digital supply chains. This integration improves traceability, predictive maintenance, and qualification speed.
- Increased Adoption for Spare Parts: On-demand manufacturing of legacy system spares using 3D printing is becoming standard practice across defense branches. A 2024 DoD inventory review reported that 15% of legacy aircraft parts were reproduced by qualified additive systems. The Air Force Life Cycle Management Center authorized 3D-printed support brackets for legacy fighters under Technical Order updates in 2023. Navy pilot programs are field-printing replacement components aboard ships, reducing downtime by 18%. Legal acceptance criteria in MIL-STD-3012 now include additive part equivalency pathways. The 2025 VP-E section of the DFARS update requires contractors to maintain certified digital design repositories. This trend ensures sustainment of aging platforms and more resilient logistics chains.
- Use in Hypersonics and Space Defence: Additive manufacturing is crucial in developing parts for advanced hypersonic and space defense systems. In October 2023, DARPA awarded grants for printing high-temperature alloys used in hypersonic airframe test structures. The Air Force Space and Missile Systems Center qualified 3D printed thruster components for future satellites in early 2025. MIL-SPEC revisions in 2024 now endorse additive materials capable of withstanding up to 2000-C for space applications. Patent filings for 3D-printed hypersonic missile casings rose 40% between 2021–2024. A classified DoD study (FY 2023) concluded that printed conformal cooling channels improve rocket motor efficiency by 15%. Legal export-control definitions under ITAR Part 121 were updated in 2024 to include additive-produced space components, enabling regulated technology sharing with allies.
Report Scope
Area of Focus |
Details |
Market Size in 2025 |
USD 3.46 Billion |
Expected Market Size in 2034 |
USD 18.36 Billion |
Projected CAGR 2025 to 2034 |
27.21% |
Dominant Region |
North America |
Fastest Growing Region |
Asia-Pacific |
Key Segments |
Offering, Process, Application, Platform, Component, End User, Region |
Key Companies |
Lockheed Martin Corporation, 3D Systems Corporation, Desktop Metal, Inc., SLM Solutions Group AG, Stratasys Ltd., General Electric Company, Boeing Company, Dassault system SE, Materialise NV, HP Inc., ExOne Company, Proto Labs, Inc., Renishaw plc, Trumpf GmbH + Co. KG, Materialise NV, Optomec, Inc. |
3D Printing in Defence Market Dynamics
Market Drivers
- Customization of Equipment: 3D printing enables tailored gear and protective equipment customized to individual soldiers’ ergonomic needs. The U.S. Army’s Soldier 1.5 program piloted 3D-printed custom knee braces in 2023, improving fit and reducing injury rates by 12%. A 2024 RAND Corporation review, commissioned by DoD, confirmed better soldier performance when using personalized, additively fabricated components. New procurement guidelines under the FY 2024 NDAA allow unit-level customization without extensive contract modifications. The Marine Corps field-tested custom-fit helmet liners made via selective laser sintering, reporting improved comfort and reduced injury claims. According to DoD medical readiness data, these implementations have reduced musculoskeletal complaints by 8%. Legal indemnity adjustments now include additively manufactured personal protective equipment under federal tort frameworks.
- Operational Readiness: Additive manufacturing enhances operational readiness by enabling rapid part replacement and recovery. In 2024, the Army Aviation and Missile Command established an AM facility at Redstone Arsenal, reducing helicopter downtime by 25%. Maintenance logs indicate 3D-printed rotorcraft spares rapidly returned aircraft to service—cutting ground time in half. A DoD Auditors’ report in 2023 highlighted improved mission-capable rates when field units used local printing resources. Regulatory updates in DFARS (2025) streamline contracting for expeditionary additive capabilities. During JRTC rotations in early 2025, units using AM reported logistic tailors being reduced by 30%. Legal supply-chain resilience mandates in the 2024 NDAA encourage wider operational integration. This driver directly translates to more available systems in critical scenarios.
- Government Incentives & Funding: Defense additive manufacturing has enjoyed ongoing federal incentives and funding. The FY 2024 budget proposed $0.15 billion in additive printing modernization for the Army, Navy, and AFRL. The tax code associated with the Inflation Reduction Act (2022) contains allowances for accelerated depreciation by the contractors that use additive manufacturing equipment in government contracts. In 2023, the National Institute of Standards and Technology (NIST) granted funding for university/industry partnerships to fill gaps in defense-grade materials qualification. The FY 2024 NDAA included a “National AM Advancement Fund” that allowed low-interest loans to defense-related small businesses. The DoD mandated in the FY 2024 NDAA that 30% of fabrication purchases include additive materials from domestic sources, under the Buy American Act, that promote reinvestment in the US. Compliance guidance on legal procurement issues, signed in 2024, can offer assistance with incentivized programs by guaranteeing transparency in the programs and laws protecting private-sector intellectual property (IP) concerns so government contractors are incentivized to decline work minimums, limiting acceptance to substantial projects.
- Reduction in Waste Material: Additive manufacturing offers a major reduction in waste materials in comparison to the traditional, subtractive works the DoD is still utilizing across sectors. A study from the Army Corps of Engineers released in 2023 discovered that metal printing reduced the amount of raw material by as much as 60%. According to Navy shipyard data from 2024, accounts for powder reuse across build batches have shown a reclaim rate over 85%. Environmental Impact Assessments for military-based projects have added analysis for AM projects to demonstrate the benefits of waste reductions as part of the overall Waste Reduction Plan, pursuant to DoD Directive 4715.26. The 2024 NDAA also expanded legal procurement requirements for contractors to use processes that are low-waste in regimes of defense contracts.
Market Restraints
- Slow Print Speeds for Mass production: While additive manufacturing is perfect for low volume needs it is short concerning build rates for mass production. The Navy conductecd official logistics analysis in 2023 which demonstrated that it takes 10-12 hours to print one metal gearbox housing. And, in the GAO Weapon Systems Annual Report (2024) it states that traditional methods still take less time to produce more than fifty items, and the structure of the Department of Defense's fourth estate acquisition is also limitedvfor using AM because of importance to that activity (DFARS, 2024). Air Force air depot managers report usual print speeds of 20-30 cm³ per hour, which is not fast enough to support the rapid fleet wide needs of the Air Force. And most attempts to parallelize additive, such as using two printers, requires double the number of energy approvals and floor space approvals. Stated outraight, AM is not currently practical for mass-production, limiting its scalability in multi-tier production of national defense contracts.
- Regulatory & Compliance Barriers: Regulatory constraints, along with rigorous quality assurance & quality verification processes impose barriers to faster adoption of defense additive manufacturing. The Department of Defense (2023) Additive Manufacturing Strategy reported that MIL-STD-3010 and quality assurance testing takes months for each part. Additionally, in the policy as a result of the DFARS update for 2024, each part must be separately qualified in the definition of part. Even the shape and geometry can possibly require a different qualification which delays timelines for getting parts into the fleet. When the GAO audits of the department covering 2022-2024 were conducted the number one obstacle to scaling was the complexity of regulatory issues. The Air Force Safety Center states that certification of critical printed parts can require over 200 document revisions and redesigns. U.S. Military Specification revisions now require additional non-destructive inspection records for each build. Legal liability frameworks under the Federal Tort Claims Act complicate field adoption without full certification. These barriers slow time-to-field delivery despite technical feasibility.
- Resistance from Traditional Defense Suppliers: Legacy defense suppliers often resist additive adoption due to business risk and disruptive change. Several major OEMs have issued warnings since 2023 that printed parts may undercut long-term service contracts. DoD contracting officers report supplier pushback during bid adjudication, citing fear of revenue reduction. The Defense Contract Audit Agency observed “sustainers” lobbying to include AM-exclusion clauses in Requests for Proposal. Legal memoranda from 2024 highlight antitrust scrutiny over exclusive AM adoption clauses that favor new entrants. Some legacy firms have attempted to delay contracts using IP and data-rights disputes. This resistance hampers government efforts to fully integrate additive into existing supply chains. Mitigation requires legal reform to balance innovation and incumbent interests.
Market Opportunities
- Smart Munitions via AI + 3D Printing: The advent of AI and additive manufacturing is yielding new capabilities for smarter and more adaptable smart munitions. Defense researchers are using AI to design optimized parts for weapons systems, detect flaws while parts are being printed, and improve precision with material flow. In recent demonstrations, AI-guided additive systems reduced scrap rates by up to 25% during missile component fabrication. The Department of Defense has launched efforts to embed machine learning into additive processes, enabling predictive analytics and better lifecycle control. Under the FY 2024 NDAA, contractors are permitted to certify AI-integrated AM workflows, making them more viable for high-risk applications. These technologies also allow for potential embedded digital twins, and automated performance tuning at the point of manufacture and of course the new technologies support precision strike battlefield capabilities with the development of faster, smarter, and more efficient munitions.
- Remote Defense Infrastructure via Large-Format Printing: Large format 3D printing is enabling mobile defense infrastructure and the ability to rapidly print critical infrastructure in rural and contested areas of operations. Trials performed in 2025 demonstrated that military formations could deploy mobile concrete printers in theater and build a bunker, barrier, or shelter, at their location. The advantage is reducing the logistics burden of moving a massive pre-fabricated structure to a remote site. Newer guidance from the DoD includes updates to do related to and found at military construction regulations. Large-scale printers can now be utilized under military engineering using mobile printers and printing with local aggregates or recycled material which is align with environmental regulation and compliance under DOD Instruction 4715.26. Units deployed in austere environments can build facility's that are mission capable within days, increasing the operational readiness of the unit. The ability to print infrastructure when needed or when deployed is changing the military's ability to respond with urgency when building bases.
- Submarine and Naval Applications: Additive manufacturing is revolutionizing naval operations by streamlining the production of complex components for submarines and warships. The U.S. Navy has begun integrating 3D-printed metal and composite parts into Columbia-class submarines, helping bypass traditional casting bottlenecks. Onboard printers are now being tested to allow crew members to produce replacement parts while deployed at sea. These capabilities reduce turnaround times for critical repairs and enhance mission flexibility during long-duration deployments. Updated acquisition rules in 2024 officially allow AM parts to substitute traditional components under MIL-STD specifications. Certified naval shipyards have expanded their printer fleets to meet growing demand for validated AM parts. This opportunity enhances fleet readiness, lowers long-term maintenance costs, and supports distributed manufacturing across the naval industrial base.
Market Challenges
- Printer Maintenance in Remote Environments: Recent advances in AM system capabilities are limited by meeting maintenance requirements in austere locations. Reports of field trainings related to 3D printing, provided in 2024, show that untrained personnel have difficulty with both calibration and basic compressor maintenance, resulting in up to a 30% workflow halt when using a printer. Spare part kits are big and, given supply chain burdens, the maintenance contracts provided through the DoD logistics extensions are experiencing low priority, with an estimated wait of 6 to 8 weeks for parts. The 2023 review by the GAO encouraged the development of ruggedized support systems, as well as remote diagnostics tools. The FY 2025 NDAA directed the DoD to set up contractor-manned maintenance hubs in theatre to shore up printer maintenance. The recent requirements in legal services contracts also dictated that when DoD is deployed, the contractor must respond to printer failures within 24 hours in deployment zones. Personnel cannot maintain the 3D printer in a forward area without fully trained technicians that have access to spare parts, so it is still an underutilized asset for units. When combined, this hurdle practically limits the Department of Defense's viable options to leverage AM during extended construction operations.
- Environmental Impact of Some Materials: Some additive manufacturing materials pose environmental and health concerns. Official Navy testing in 2023 revealed that certain metal powders emit fine particulates during reuse cycles, requiring specialized filtration systems. DoD Directive 4715.26 now mandates monitoring of powder handling operations, with stricter controls added in 2024. The Air Force Occupational Safety Office has recorded two instances of worker respiratory irritation linked to polymer fumes in 2024. Environmental impact studies show that recycling metal powder consumes up to 20% more energy than virgin production in some AM processes. The National Defense Authorization Act tasks DoD with reassessing chemical safety protocols for AM materials biennially. These factors necessitate investment into safe handling and containment infrastructure.
- Dependence on Foreign Raw Material Supplies: The additive manufacturing capabilities of Defense remain at risk largely because the United States has to import the powders and polymers from foreign suppliers. The most recent briefing from the DoD recently confirmed that about 70% of high-performance titanium and nickel alloy powders are produced by suppliers in China and Russia. The FY 2024 NDAA directed to the DoD to establish domestic powder production capabilities, but pilot production facilities just began operating in early calendar year 2025. Absent any substantial domestic production capability, No DoD programs can avoid disruption due to geopolitical export control or sanctions that could affect their ability to compete with domestic capability.
3D Printing in Defence Market Segmental Analysis
Offerings Analysis
Printer: The printers segment dominated the market in 2024. 3D printers enable defence additive manufacturing when applied to making end-use components, prototypes, and mission essential tools at the point of need. From small field-deployable FDM systems that fit in a backpack to a large industrial-grade PBF machine or DED system that can yield tonnes of functional raw materials, defence agencies are utilizing a spectrum of hardware to allow them to fulfil operational requirements. These systems produce parts for vehicles, aircraft, and even field hospitals, significantly reducing logistics burdens. The strategic importance of having on-site, ruggedized printing capabilities—especially during prolonged missions—has made printers an essential investment across land, naval, and aerospace applications.
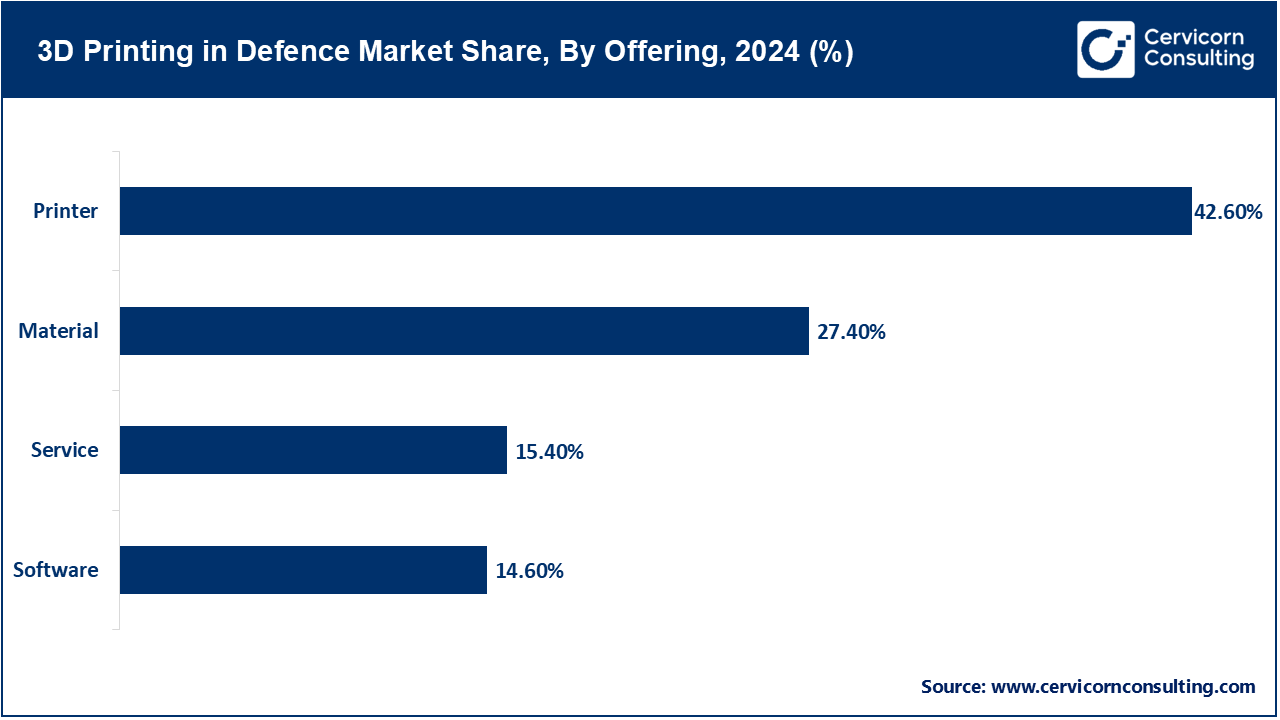
Material: Materials in the defence 3D printing domain range from high-strength metals like titanium and Inconel to composite polymers and fiber-reinforced resins. Each is selected based on mission-critical requirements like thermal stability, weight reduction, and mechanical resilience. For instance, aluminium alloys are favored for aircraft parts, while steel composites suit naval applications. The military's increasing focus on localized manufacturing requires secure, validated supply chains for certified material input. Software: Software serves as the digital foundation for defence additive workflows, converting CAD outputs into printable formats while maintaining acceptable military standards. Software platforms provide print path enhancement, structural simulation including performance, and topology optimization for weight reductions. The latest advancement leverages AI-powered functionality to offer predictive maintenance and build-failure prevention operating at machine, sequence and process levels, thus minimizing waste and maximizing uptime. Ability to build tighter integration into existing battlefield logistics systems will afford engineers working from their office desks a meaningful ability to collaborate with Teams in the field. Increasingly, defence software includes cybersecurity layers to prevent IP theft or sabotage—making it indispensable in secure, scalable manufacturing operations.
Services: Services provided in defence 3D printing vary and may include end-to-end production assistance, design consultation, materials testing, and post-processing for components used in an environment where there is a risk to the workspace. Providers, in-house or contracted, will have access to different workflows tailored for weapon components, airframe reinforcements, or surgical implants. Mobile AM Labs (often containerized) can support frontline units with repairs and custom part requests. With collaboration arrangements in place with the national labs and academic institutions, the possibilities of accelerating R&D development are enhanced. All of these services are intended to facilitate deployment readiness, decrease lead times, and ensure Armed Forces are in a position to produce and fabricate mission-specific tools or components, even in austere and high-threat locations.
Process Analysis
Binder Jetting: Binder jetting is primarily used in the defence sector for prototyping, design validation, and low-density part fabrication. The process binds powdered material using a liquid agent, creating models quickly without high heat. Though not ideal for load-bearing parts, binder jetting supports educational tools, training devices, and low-strength functional components. With post-processing like sintering, some metal parts can gain enhanced strength. Defence designers use this technique for aerodynamic models, mock-up equipment, or pilot-testing new designs before transitioning to high-performance production methods like PBF or DED.
Direct Energy Deposition (DED): DED excels in producing large, durable parts or repairing worn-out components directly on existing structures—a major benefit for aircraft, vehicles, and naval systems. The method uses a laser or electron beam to melt wire or powder feedstock, allowing flexible geometry and gradient materials. Its high deposition rates are suited for rebuilding turbine blades or custom tools in limited-time missions. In defence healthcare, it’s even used to repair surgical instruments. The advantages of DED are restoring critical components instead of having to freeze the asset and purchase a whole new part, resulting in extended uptime and reduced waste across the supply chain.
Material Extrusion: Material extrusion (FDM) is a robust system that is cheap and flexible. In defence, it produced a great deal of rapid prototype which allowed realistic amounts of UAV shells to be developed, soldier systems, or electronics mounts on soldier equipment while still having rugged properties. If the parts are not war-critical, extruding using base or mobile facilities could yield great time savings and allows for ease of logistics since no specific technical requirements are required to use ABS, nylon, or fiber reinforced composites. Material extrusion will not yield the tolerances of PBF or SLA but is excellent for iterative development that created tactical tools quickly. Its ease of use makes it a preferred solution in field-deployed AM units.
Powder Bed Fusion (PBF): The powder bed fusion segment has dominated the market in 2024. PBF, including Selective Laser Sintering (SLS) and Direct Metal Laser Sintering (DMLS), is a key method for manufacturing high-strength, complex defence components. It allows production of lightweight, structurally sound parts like drone brackets, missile components, and aircraft joints. Materials like titanium and Inconel provide necessary thermal and fatigue resistance. PBF also supports lattice structures for shock absorption and stealth. Due to its precision and mechanical reliability, PBF is increasingly integrated into defence production lines, especially in air and space domains requiring tight tolerances.
Sheet Lamination: Sheet lamination is used for educational and planning models within the defence sector, building objects by bonding layers of material sheets. Though limited for structural parts, it excels in creating low-cost, low-waste training aids, tactical maps, and field mock-ups. Command centers use laminated models to simulate terrain or rehearse mission scenarios. Its fast output and minimal infrastructure make it suitable for pre-deployment exercises. In military healthcare, laminated anatomical models support surgical planning and personnel education, especially in resource-constrained environments.
Application Analysis
Functional Part Manufacturing: The functional part manufacturing segment dominated the market in 2024. Functional part manufacturing within the defence function focuses on manufacturing fully deployable parts like missile cases, frames for vehicles, fuselage sections of unmanned aerial vehicles (UAVs) and turbine parts for aircraft. These mission-critical, end-use parts are printed using high-strength alloys through a number of advanced processes including Direct Metal Laser Sintering (DMLS) and Electron Beam Melting (EBM) to survive in operations. There is plenty of room for additive manufacturing to have a consequence in producing parts through a process called topology optimization and weight reduction while enhancing or maintaining performance. Additive manufacturing has the added benefit of reducing dependencies on supply chains during warfare or expeditionary force deployments, enabling on-time manufacturing, field maintenance, and spare part replacement in urgent scenarios.
3D Printing in Defence Market Revenue Share, By Application, 2024 (%)
Application |
Revenue Share, 2024 (%) |
Functional Part Manufacturing |
54.20% |
Tooling |
20.30% |
Prototyping |
25.50% |
Tooling: Tooling in the 3D printing defence market is a large benefit for the production of jigs, gauges, molds and dies when dealing with high levels of dynamic precision to assemble, align, or repair complicated weapons systems and COMBAT platforms. Often custom-made to fit unique geometries such as tanks, aircraft, or missile systems, tooling processes through 3D printing allow designs that reduce tolerance errors and maximize efficiency in assembly work. 3D printing also has the potential to reduce tooling lead times from several weeks to a few hours, improving repair cycle capabilities and rotating staff at field depots. Common tooling materials withstand operational wear, rugged composites include carbon-fibre and heat-resistant polymers. Extra benefit is its ability to add modularity and scalability by fitments through the various complex geometries related to different operational profiles, increasing the responsiveness to missions and mission readiness.
Prototyping: Prototyping is one of the most important defence applications of 3D printing, allowing for quick turnaround on design iterations for new equipment like unmanned systems, advanced weapon systems, or soldier-worn equipment. CAD-based processes let designers and engineers make, test and change parts before investing time and money in final production. This reduces R&D costs and time-to-deployment. Prototypes are evaluated for aerodynamics, heat resistance, and weight using real-world simulations. Importantly, on-demand prototyping enables combatant commands to co-develop and test gear in theater, fostering a soldier-driven innovation model that aligns with defence modernization priorities.
Platform Analysis
Airborne: 3D printing in airborne defence platforms supports the production of lightweight, structurally resilient parts for fighter jets, helicopters, and drones. Components such as avionics housings, ductwork, and radar mounts are printed using titanium or PEEK-based polymers for high strength-to-weight ratios. Additive manufacturing reduces lead times for mission-critical replacements, especially for legacy aircraft with obsolete components. Onboard diagnostics linked with AM allow predictive replacement of failing parts, improving flight-readiness. The U.S. Air Force and Boeing have both adopted 3D printing for rotorcraft parts and structural brackets, validating its importance in aerial defence logistics.
Land: The land segment has accounted highest revenue share in 2024. The land domain benefits from the use of additive manufacturing, through local production of vehicle armor, gun mounts, replacement gears and even drone parts intended for specific terrain. Army forward operating bases are now employing containerized AM labs, allowing them to locally fabricate the damaged and missing parts directly in combat zones. These systems are using durable materials–such as nylon composites or Inconel–to improve the durability of its supply chain during extended operations and contested environments. The additive solutions are also being used to support refurbishment of tanks, higher capability for engineering vehicles, and even repair of powertrains in armored carriers. Overall, additive manufacturing enables ground forces to remain operationally agile and keep continuity with limited logistic support.
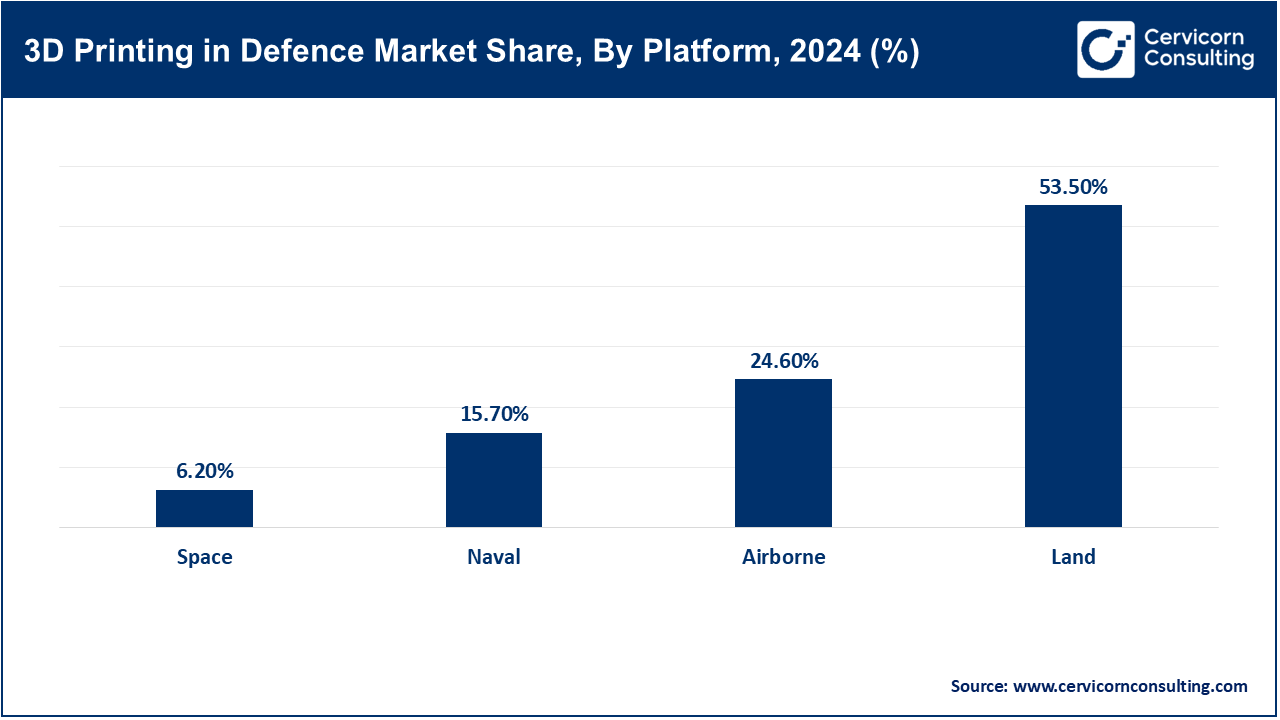
Naval: 3D printing is being used to manage maintenance and sustainment of parts on-board warships, submarines and other maritime vessels/stations. For example, AM systems installed into naval vessels are used to fabricate replacement parts for valves, brackets and pump impellers as well as medical or cooking tools for the vessel. The systems must function reliably in very corrosive environments and extreme vibration. Notably, the focus on metal printing is growing in naval vessels for replacement parts like propeller blades and hydraulic components. The U.S. Navy has tested 3D-printed metal drain strainers aboard the USS Harry S. Truman, demonstrating readiness for permanent part replacement at sea. Additive printing reduces downtime and eliminates port-dependency for basic inventory.
Space: 3D printing for defence-related space applications supports satellite components, antenna arms, brackets, and shielding elements. Several defense agencies including the U.S. Space Force and NASA are collaborating with private aerospace companies to implement additive manufacturing on orbit-capable vehicles. The key benefits of using 3D-printed parts is the ability to consolidate designs and to optimize weight, both of which are critical issues on launch vehicles. Additionally, NASA and the Department of Defense are working on autonomous manufacturing and the potential of in-space manufacturing in orbit.
Component Analysis
Technology: The technology segment has held dominant position in 2024. Within defence 3D printing, technology encompasses all aspects of the hardware (printers), software, monitoring systems, and integration platforms utilized to produce output suitable for mission. Typically, printers either tend to be smaller, lightweight ruggedized FDM printers which have been produced specifically for battlefield use, and, large-scale high-power laser sinters which are used to operate centralized production facilities. Defence-specific software handles STL editing, thermal analysis, and transfer of design files from a cybersecure stand point. Artificial intelligence algorithms also contribute to optimizing build orientation and materials where possible. As all of these technologies are enhancing their capabilities, Integrated sensors assures process traceability and repeatability. While functions of field-deployable (tech) is improving, the military is becoming more inclined toward plug-and-play type units requiring less training and work more successfully in an environment where temperatures and other environmental stressors are outside a 'friendly' range.
3D Printing in Defence Market Revenue Share, By Component, 2024 (%)
Component |
Revenue Share, 2024 (%) |
Technology |
47.20% |
Material |
34.20% |
Services |
18.60% |
Material: Materials, along with the technology component, occupy critical positions in the defence 3D printing ecosystem, materials need to gain trust and rigour to comply with MIL-STD certifications and provide resilience in the form of thermal, mechanical, and environment standardization, titanium, aluminum alloys, inconel, and cobalt-chrome are materials that are commonly utilized, and can be used for aircraft and missile construction, as contrast, carbon fiber, polyetheretherketone (PEEK), and glass filled nylons can be selected for high-performance lightweight structures. They must support a high fatigue performance level and material engenders good results in performance strength and corrosion-resistant nature, along with some stealth features. As a research and development effort, there is a trial for producing materials for EM shielding, and radar absorption characteristics. The military is also developing materials that lend all the advantages of military-grade printables, and this is sending a strong signal that AM is now increasingly supplanting the traditional approaches to manufacturing in frontline production points.
Services: 3D printing services in defence cover pre-print design, material validation, post-processing, real-time diagnostics, and regulatory compliance support. Companies like Lockheed Martin and Stratasys offer on-site AM labs and digital platforms to field units, enabling fast production and repair services. Military bases benefit from support in scanning broken components, reverse engineering, and applying proper thermal or surface treatment post-print. Service providers also manage secure data handling, vital for defence IP protection. These services bridge the gap between frontline needs and centralized production capabilities, allowing flexibility across multiple theatres of operation.
End-Use Analysis
Army: The army segment has leading the market in 2024. The United States Army employs 3D printing, or additive manufacturing (AM), to establish supply lines, manage logistics, expand repair options, and produce applicable components for the battlefield. AM is utilized to create parts for vehicles, the housing for weapons, and wearable armor. Mobile AM units operated from forward bases will improve operational effectiveness for losses that are less damaging than losses that require advantage at sea or by air. The Army's "Jointless Hull" project, which utilizes large-scale additive capacity systems to produce a full vehicle structure, demonstrates something that creates significant opportunities for new possibilities. The Army is also experimenting with 3D printing food utensils, medical equipment, and drone airframes on multi-material platforms. The Army indicates additive manufacturing represents offense for ground forces and phase II of its readiness and future fight system.
3D Printing in Defence Market Revenue Share, By End Use, 2024 (%)
End Use |
Revenue Share, 2024 (%) |
Army |
39.70% |
Navi |
34.50% |
Airforce |
25.80% |
Navy: The Navy has embraced 3D printing, AM, to sustain maritime fleets of ships, submarines, and aircraft, even if they cannot always get a ship back to a nearby dock. Typical onboard shipboard systems will print pump parts, electrical enclosures, and surgical implements to support needs during long deployments. Navy engineers are exploring other consumables, such as heat exchangers, and entire replacement gearboxes comprised of 3D printed components. Central hubs have also been established at every naval base, with some bases acting as enterprise-sized machines to support post-part deployments production and training. The Navy emphasizes reliability, especially for parts being used in ships that may also be operating under the pressures of vibration, salt, and temperature changes. The integration of 3D scanning and additive systems aboard Navy ships (i.e., carriers) will ease life cycle maintenance while comfortably evolving workflows toward the navy of the future, characterized by modernization and autonomous and artificial intelligence-based support.
Airforce: The Air Force integrates 3D printing to produce lightweight airframe components, customized cockpit controls, and in-flight testing fixtures. With rapid turnaround required for airborne platforms, the service uses metal and composite AM to replace aging aircraft parts quickly. The USAF has even deployed AM systems in maintenance hangars for on-the-spot component recreation. Additive technologies are also used in simulator training, facial reconstruction for injured pilots, and G-force test devices. These advancements support the Air Force’s goals of agile logistics, predictive maintenance, and resilience in advanced aerospace operations.
3D Printing in Defence Market Regional Analysis
The 3D printing in defence market is segmented into several key regions: North America, Europe, Asia-Pacific, and LAMEA (Latin America, Middle East, and Africa). Here’s an in-depth look at each region.
Why is North America leading the 3D printing in defence market?
- The North America 3D printing in defence market size was valued at USD 1.30 billion in 2024 and is expected to reach around USD 8.34 billion by 2034.
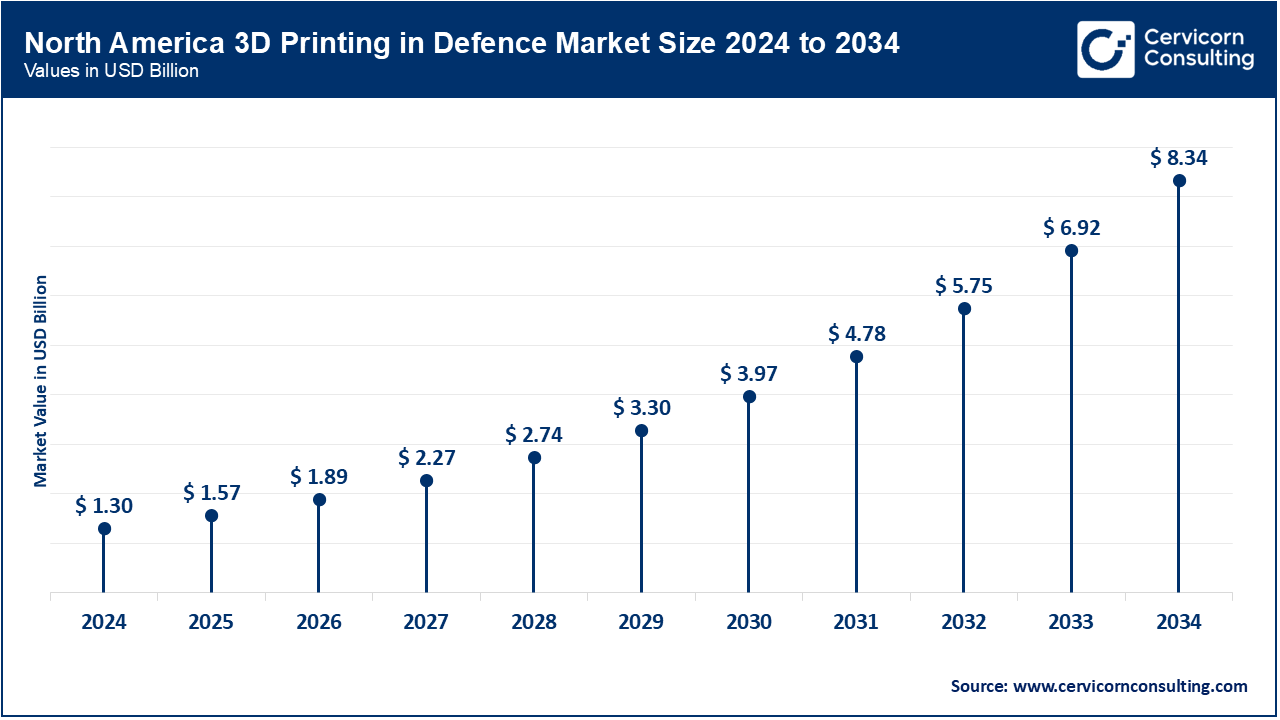
North America is the leader the market thanks to a strong defense health ecosystem, favorable FDA regulations, and early adoption to advanced manufacturing technologies. The U.S. Department of Defense continues to support the research of medical AM through DARPA, the VA system, and military research and development labs. Hospitals and military bases use AM for personalized implants, surgical guides, and tools for treating traumas. Canada also supports biofabrication through institutions like the NRC. The combination of strong investments, regulatory interpretations, and public-private approaches allowed North America to have a competitive edge in the 3D printing for defense-health.
Why is Europe demonstrating clear growth in the 3D printing in defence market?
- The Europe 3D printing in defence market size was estimated at USD 0.75 billion in 2024 and is projected to surpass around USD 4.83 billion by 2034.
Europe is demonstrating clear growth in market with nationalized healthcare systems, NATO led defense innovation, and regulatory standardization through EU regulation. Military medical innovation is occurring in Europe, specifically in Germany, UK, and France with 3D printing being integrated with field hospitals and rehabilitation facilities. The EU MDR provides clear guidelines for printed medical devices that can be utilized in a safe manner. The third convergence of defence-health can be seen in collaboration projects being funded by Horizon Europe and the EDA.
3D Printing in Defence Market Revenue Share, By Region, 2024 (%)
Region |
Revenue Share, 2024 (%) |
North America |
45.40% |
Europe |
26.30% |
Asia-Pacific |
18.90% |
LAMEA |
9.40% |
Why is Asia-Pacific developing quickly in the 3D printing in defence market?
- The Asia-Pacific 3D printing in defence market size was reached at USD 0.54 billion in 2024 and is anticipated to grow around USD 3.47 billion by 2034.
Asia-Pacific is a region that developing quickly in market, supported by increased defense budgets, expanding healthcare infrastructure and technology initiatives to help develop within the countries. Nations like China, India, Japan, and South Korea have increased funding for military medical modernization, dividing their AM initiatives, such as deploying AM within military field hospitals and disaster settings. China has made enormous advances to develop bio-printed organ research, while India has had AM introduced within their armed forces medical colleges. Regulatory pathways have begun to open, and involved countries are building a framework and policy for biocompatible and trauma-response tools. The Asia Pacific region also has the added benefit of very low-cost production and vast volume scalability.
LAMEA 3D Printing in Defence Market Trends
- The LAMEA 3D printing in defence market size was accounted for USD 0.27 billion in 2024 and is expected to grow around USD 1.43 billion by 2034.
LAMEA indicates developing intent to explore 3D printing for the health sector, dedicated focus on in the humanitarian context and military field medicine. Within the Middle East, the UAE and Saudi Arabia are leading the way concerning investment in smart healthcare and military battlefield readiness, which includes mobile AM labs and surgical models. Now there is also pilot testing to develop low-cost 3D printed prosthetics and 3D printed anatomical training models with military hospitals in Latin America. Throughout Africa, examples of NGOs and UN missions are happening now in the forefront of using 3D printing for trauma and orthopedic training/care, support provided in remote conflict zones. As and example, charity bodies have limited infrastructure, and potential, but innovation hubs are rapidly growing, almost weekly.
3D Printing in Defence Market Top Companies
Recent Developments
Recent partnerships in the 3D printing in defence industry highlight innovation and deepening defense-tech convergence. Lockheed Martin has expanded its collaboration with Sintavia to develop 3D-printed aerospace components with enhanced thermal and structural performance. Stratasys has partnered with the U.S. Navy to deliver deployable 3D printing units for shipboard part manufacturing. 3D Systems works with the U.S. Army on metal AM for lightweight, durable combat vehicle parts. Desktop Metal collaborates with the Department of Defense to scale binder jetting for high-volume part replacement. SLM Solutions partners with Honeywell for aerospace certification of printed parts. These alliances are accelerating precision, autonomy, and supply chain resilience in defense production.
- In March 2024, GE Aerospace is investing over $0.65 billion in 2024 to expand its global manufacturing plants and supply chain, with a major focus on scaling up production of 3D printed jet engines such as the LEAP and GE9X models. This investment will fund new 3D printers, tooling, and facility upgrades across multiple U.S. and international sites, aiming to meet rising demand from commercial and defense clients. The LEAP engines, produced with CFM International, already power major aircraft and use 3D printed fuel nozzles that boost efficiency and durability, while the GE9X engine for the Boeing 777X features over 300 3D printed parts, enabling complex geometries and improved fuel efficiency. The expansion will also create over 1,000 new jobs and further solidify GE Aerospace’s leadership in additive manufacturing as it becomes an independent company.
- In September 2022, Nikon Corporation announced a $0.622 billion takeover of Germany’s SLM Solutions Group, a leading metal 3D printing machine manufacturer, in September 2022. The acquisition process, which included a public tender offer at a 75% premium over SLM’s previous share price, was supported by SLM’s key shareholders and completed in January 2023, making SLM a consolidated subsidiary of Nikon. By September 2023, Nikon finalized the squeeze-out of minority shareholders, fully integrating SLM into its digital manufacturing strategy as Nikon SLM Solutions AG. The move combines SLM’s advanced metal additive manufacturing technology with Nikon’s expertise in opto-electronics and precision equipment, aiming to accelerate innovation and revolutionize global mass production in digital manufacturing.
- In October 2023, Boeing has started 3D printing parts for the AH-64 Apache helicopter to cut long lead times and improve supply chain resilience. In partnership with ASTRO America, it used the world’s largest metal 3D printer at Rock Island Arsenal to create a main rotor link from 6000-series aluminum in just eight hours—a task that usually takes a year with forging. A fully 3D-printed rotor system will be tested in spring 2024. While forging remains ideal for mass production, 3D printing offers speed and strength benefits for critical, low-volume parts. This effort is part of the U.S. Army’s $0.095 billion Jointless Hull Project.
Market Segmentation
By Offering
- Printer
- Material
- Software
- Service
By Process
- Binder Jetting
- Direct Energy Deposition
- Material Extrusion
- Powder Bed Fusion
- Sheet Lamination
By Application
- Functional Part Manufacturing
- Tooling
- Prototyping
By Platform
- Airborne
- Land
- Naval
- Space
By Component
- Technology
- Material
- Services
By End-Use
By Region
- North America
- APAC
- Europe
- LAMEA
...
...